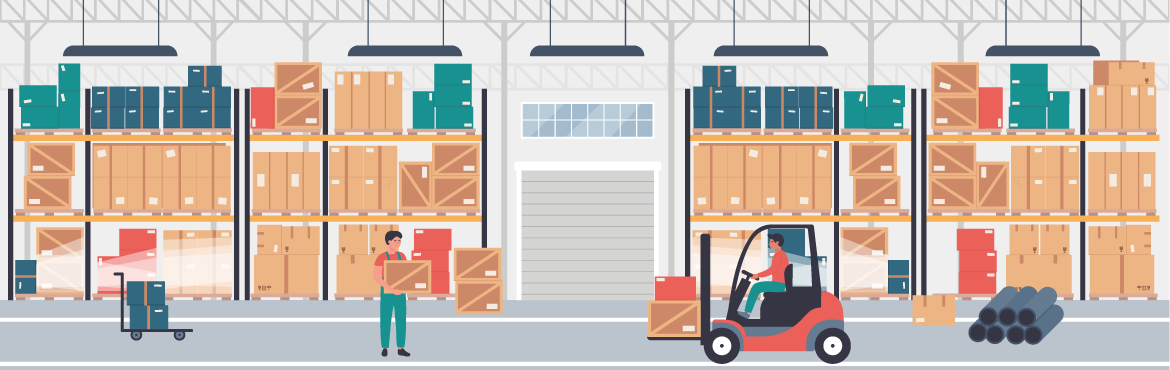
Item master is at the heart of all the transactions. Sales, Purchase, Production, Quality etc. all depend on this master.
Setting the item master correctly and completely will help you to extract most from OurSys ERP.
The Customer Master
All inventory items such as finished goods, sub-components, raw material, packing material, tools, toolings, consumables are all part of the same item master.
Unique identification and codification is critical for inventory management using any ERP system. But in this article we are going to discuss the sub masters of Item master.
Here are some important sub-masters related to OurSys along with their importance. We request you to update your item master wherever the data is incomplete or incorrect.
Sub-Masters of Item master
Item Category Master
Inventory items are broadly categorised as Raw Material, Finished Goods, Semi-Finished goods etc. All these are defined in the Item Category master.
OurSys comes with default categories but you can add further sub-categories as required. All inventory reports are filtered based on this categorisation. Some fields of Item master also change based on the Item Category selected.
Unit of Measurement Master
The unit of measure for every items is the unit in which the inventory of that item is maintained. OurSys comes pre-loaded with common unit of measurements but you can add more.
One item can have multiple units of measurement but one of them has to be marked as default.
Inter conversion between these units for a particular item is also available in OurSys.
Sales Category Master
Sales Category is different from Item Category. It is the category of finished products as defined by the company on their websites and sales catalogues.
You will know which category of products are performing well and which are not once you do this categorisation. You can also set category wise sales targets for the sales representatives.
Planning Category
By default it is marked as MRP which means that the requirement will be generated through the MRP program.
The other option is 'Replenishment'. When you select this option, you can set minimum and reorder level for the item. Items below the levels appear in the dashboard automatically.
Default Storage Location Master
This master is a list of all the storage locations. It covers all drawers, racks, pallets, open spaces etc. In case you prefer a particular location for storing an item, you must select that location for the item in the master.
During 'Putting' process, the putting location is prefilled automatically based on this selection. Also, putting list printout will have this location name which will help the store keepers to keep the material at the right location.
HSN Master
This is the list of applicable HSN number.
While invoicing, this HSN is automatically selected and the corresponding GST rate gets applied.
Some other settings:
Saleable Item (Yes/No): Only items with "Yes" appear in the sales module. This eliminates the clutter and avoids mistake of choosing the right items
Purchaseable Item (Yes/No): Only items with "Yes" appear in the purchase module. Thus if a desired item is not visble in PO or PR check this setting.
Sales Minimum Order Quantity: You can mandate minimum selling quantity by entering the minimum sales figure here.
Issued as a part of Kit (Yes/No): The default is "Yes", but if mark it as 'No' then this item will be assumed to be on the line and will not be issued along with the BOM as a part of the kit.
Traceability Required (Yes/No): If marked as 'Yes', individual lots will be created everytime the item is inwarded whereas the setting of 'No' will add all inwards to the same default lot. Ideally only consumables should be marked as 'No'